Mold is a fungus that produces spores which are spread by floating around in the air. It is present in indoor environments, thriving in areas that are moist and warm. When a spore lands on a damp spot, it begins to grow, and can grow on a variety of surfaces including fabric, paper, wood, glass and plastic. Depending on the material and type of mold, it may digest the material it grows on. There are hundreds of thousands of types of mold, occurring both indoors and outdoors, and can cause a variety of health problems ranging from mild to severe. Mold prevention during the construction process is imperative to keeping your project on track and on budget.
When you are embarking on a construction project, the primary reason mold happens is because of uncontrolled moisture incursion. This can be from liquid flow, condensation, high humidity or capillary action that dampens building materials. Mold growth can start within 24-48 hours of materials getting wet, so inspections for moisture are imperative.
Major causes of mold growth during construction include site issues like poor drainage, inadequate building protection, water buildup and materials getting wet. There are also product issues (mostly wood members with lumber yard or sap-stain molds), procedural issues (not reacting to mold growth to stop it) and design issues (construction defects that allow moisture incursion).
Mold takes a variety of forms and textures. It can be white, black, yellow, blue or green and can look like discoloration or stain on a surface. It can also be velvety, fuzzy or rough in appearance depending on the type of mold it is and where it is growing.
Taking proactive measures to prevent mold during construction is crucial to ensuring you don’t have a mess on your hands down the road. Site, product and procedural issues are recognizable and can be addressed in advance to prevent mold from growing in the first place. Design flaws must be addressed as soon as they are discovered and should be immediately documented. Similarly, when a construction defect results in moisture incursion, it should be addressed as soon as it is noted. The longer moisture sits in a place, the more mold will grow. There is also the propensity for hidden growth inside walls, ceilings, floors or in layers of construction that may not be readily seen.
There are a few things you can do to be proactive in mold prevention. Develop moisture control strategies and response plans. Have water pumps, fans, dehumidifiers and wet vacs ready and on-site to help clean up water events. If this is not possible, having access to a professional contractor to bring in on such an event is vital. Protect all materials, especially porous materials like drywall and wood. These should be stored in a dry location. Arrange with your lumber supplier what will be done with lumber showing visible signs of mold growth.
If you do all of these things, you will limit your liability risk and potential litigation should a home end up with serious damage due to negligence. Another good idea for your residential builds is to incorporate dry lock, use mold-resistant drywall or sheet rock and ensure painters use mold-resistant paint. Ensure the foundation is properly poured so moisture is locked out. You may want to even use these things as a selling point for your projects. If the subject comes up, buyers will want to hear that you’ve taken proactive measures to keep mold out during the build and will have more confidence in their purchase.
Mold prevention is incredibly important when building new homes, and equally important once the build is complete. Keeping your site as moisture-free as possible, protecting your materials, reacting to any seen mold or moisture and documenting any problem areas is crucial to the success of your project. There are many people who react poorly to mold spores, which can cause a variety of health problems. Proactive preparation will help reduce and prevent mold growth.
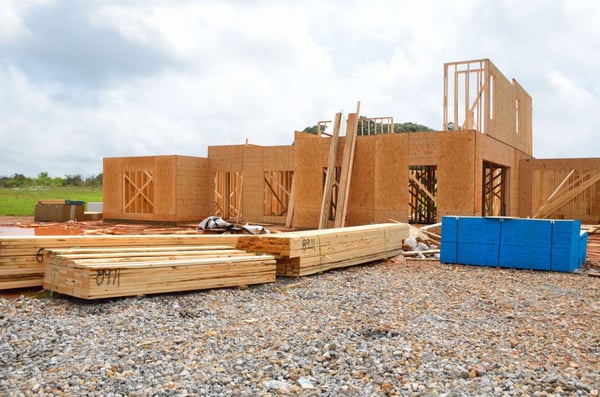
Recent Posts
- Spec Construction Loans: A Spec Line of Credit Is Worth the Paperwork
- Spec Homes and Pre-Sale Homes: The Relative Benefits for a Spec Builder
- How a Lender Sees Spec Construction Success: Insights for the Investor Builder
- How Is a Spec House Different From Other Kinds of House Construction?
- How a Private Lender Compares to a Bank Lender for a Spec House Construction Loan